Tech
Choosing the Right Hydraulic Oil for Your Machine
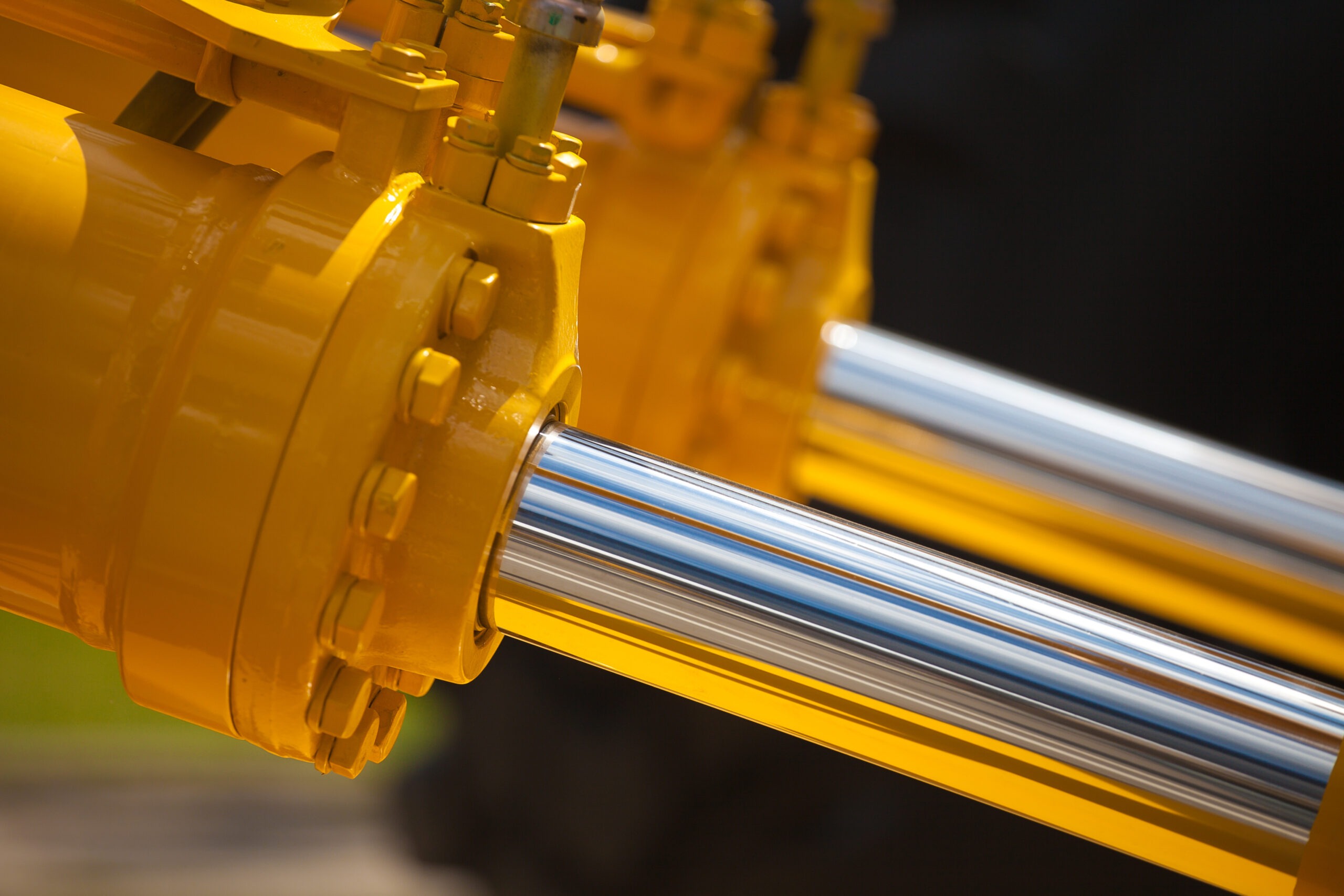
Key Takeaways
- Understanding the role of viscosity and additives is crucial.
- Compatibility with machine components should not be overlooked.
- Proper maintenance and fluid checks enhance performance.
- Consulting manufacturer guidelines ensures correct oil selection.
Understanding Hydraulic Oil and Its Importance
Hydraulic oil is often considered the lifeblood of machinery, facilitating vital operations by transferring power, reducing friction, and protecting system components from corrosion. It ensures smooth and efficient operations, playing a fundamental role in the longevity and performance of equipment. The type of hydraulic oil you choose can significantly influence machine efficiency, as well as its operational costs and downtime. Selecting the right hydraulic oil involves evaluating several factors, including the machinery type, operating conditions, and specific requirements. For those navigating the options available, including regional specifics like hydraulic oil Charlotte, NC, making informed decisions can benefit equipment performance and service life.
Additionally, the viscosity of hydraulic oil plays a crucial role in determining its effectiveness under varying temperatures and pressure conditions. Regular monitoring and maintenance of hydraulic oil can prevent system failures, extend component lifespan, and reduce overall maintenance costs. High-quality hydraulic oil for specific applications ensures optimal performance, particularly in demanding industrial environments.
The Role of Viscosity in Hydraulic Oil
Viscosity is among the most critical characteristics of hydraulic oil, playing a pivotal role in determining how well the oil can perform its function. It measures the oil’s resistance to flow, affecting the fluid’s ability to transfer power and lubricate components effectively. If the viscosity is too high, it can cause inefficient power transmission and hinder start-up operations in cold conditions. Conversely, the protective oil film could be compromised if the viscosity is too low, leading to increased wear. According to Machinery Lubrication, selecting the proper viscosity stabilizes operations and reduces wear and tear, significantly lowering maintenance costs and ensuring operational efficiency across temperature variations.
Identifying the Necessary Additives
Hydraulic oils often contain additives that enhance their performance characteristics, tailored to meet specific operational needs. These additives include anti-wear agents, which prevent metal-to-metal contact, anti-oxidants that prolong oil life, and anti-foam agents that ensure consistent performance in high-speed applications. The selection of the proper additives should reflect your machinery’s operational demands, providing the oil fits the equipment’s technical specifications and enhances its functional life. Properly chosen additives can result in extended service intervals and improved protection against component failure, providing peace of mind and a better return on investment for machinery operators.
Ensuring Compatibility with Machine Components
Compatibility between hydraulic oil and machine components is paramount to prevent degradation and ensure operational smoothness. Hydraulic oils must align with the construction materials of critical machine components, such as seals and gaskets, to avoid production disruptions due to material incompatibility or chemical interactions. Insights from the Hydraulics & Pneumatics guide emphasize the necessity of conducting thorough compatibility assessments to safeguard against potential issues arising from reactive interactions. Inadequate compatibility checks can lead to seal failures or other operational inefficiencies, emphasizing the importance of this consideration in the oil selection process.
Referencing Manufacturer Guidelines
Manufacturer guidelines provide essential insights into your machinery’s specific requirements and recommendations. These guidelines encapsulate years of product research and development, offering a tailored approach to maintaining equipment’s health and efficiency. Adhering to these guidelines ensures that you select the hydraulic oil that best complements the machinery’s operational architecture, optimizing performance and preventing unnecessary damage. By following these tailored recommendations, operators can enhance machine reliability and ensure consistency in performance over time—a critical factor for businesses focused on maintaining high operational productivity.
Benefits of Regular Fluid Checks and Maintenance
Routine fluid checks and maintenance are critical in keeping machinery in peak condition and preventing costly repairs. Regular monitoring of hydraulic oil conditions—through color, viscosity, and particle contamination observations—provides early warnings of potential machine issues. Conducting these checks allows for proactive oil quality management, ensuring the fluid remains within optimal operating parameters. Such diligence enhances machine performance and extends the equipment’s lifecycle, reducing the likelihood of unexpected breakdowns and associated costs.
Environmental Considerations
Considering hydraulic oil’s environmental impact is increasingly important in today’s industrial landscape. Choosing biodegradable oils that meet performance requirements while less environmentally harmful can help reduce industrial operations’ ecological footprints. These greener alternatives comply with stringent environmental regulations, facilitating responsible operations and enhancing corporate sustainability initiatives. Making informed choices regarding environmentally friendly oils contributes to a more sustainable industrial practice, reflecting positively on a company’s commitment to environmental stewardship.
Real-Life Examples of Hydraulic Oil Selection
Real-world examples illustrate the profound impact of selecting the appropriate hydraulic oil. For instance, a large agricultural operation initially chose an incorrect oil type, leading to increased maintenance costs and frequent breakdowns. However, upon switching to a well-suited oil with specific anti-wear additives, the operation experienced reduced downtimes and maintenance interventions. In stark contrast, another manufacturing facility optimized its hydraulic oil choice, improving production throughput and machinery reliability. This highlights the importance of proper hydraulic oil selection in enhancing operational efficiency and reducing costs, ultimately driving better business outcomes.