Business
Advancements in Plastic Welding: Applications Across Industries
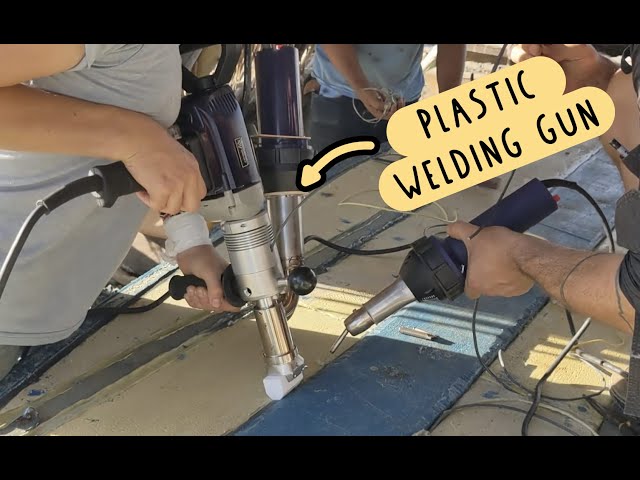
Plastic welding has emerged as a revolutionary technology, offering versatile and sustainable solutions across various industries. Unlike traditional bonding methods, plastic welding uses heat to fuse thermoplastic materials together, creating strong and durable joints. This technique has gained widespread recognition due to its cost-effectiveness, efficiency, and environmental friendliness. In this blog, we’ll explore the diverse applications of plastic welding and how it’s transforming industries.
Automotive Industry
Plastic welding has found a significant place in the automotive industry, where lightweight and durable materials are crucial for enhancing fuel efficiency and overall performance. Bumpers, interior components, and even fuel tanks can be seamlessly joined using plastic welding techniques. The process ensures a strong bond that withstands the harsh conditions experienced by automotive parts, contributing to the overall safety and longevity of vehicles.
In the automotive industry, plastic welding, often performed using specialized PVC welding rods, plays a crucial role in seamlessly joining components such as bumpers and interior parts, contributing to both the structural integrity and overall durability of vehicles.
Medical Devices
In the healthcare sector, the demand for precision and cleanliness is paramount. Plastic welding has become a preferred method for assembling various medical devices, including tubing, containers, and intricate components. The ability to create hermetically sealed joints ensures the integrity of these devices, preventing contamination and ensuring patient safety. Additionally, the process allows for the assembly of single-use medical instruments, reducing the risk of cross-contamination.
Packaging Industry
Plastic welding has revolutionized the packaging industry by providing an efficient way to manufacture secure and tamper-evident packages. From food packaging to pharmaceutical blister packs, plastic welding ensures airtight seals that preserve the integrity of the contents. The ability to work with a variety of plastic materials allows for customization based on the specific requirements of different products, contributing to sustainability efforts by reducing the need for additional materials.
Construction and Infrastructure
In the construction and infrastructure sectors, plastic welding is increasingly being used for joining pipes, geomembranes, and other structural components. The technique is especially valuable for creating impermeable barriers in civil engineering projects, such as landfill liners and reservoir linings. Plastic welding’s resistance to environmental factors makes it an ideal choice for applications where durability and longevity are crucial.
Electronics Manufacturing
Precision and reliability are key factors in electronics manufacturing, and plastic welding has become an integral part of the process. The technology is employed to assemble casings, connectors, and other components of electronic devices. Plastic welding ensures a secure and uniform bond, contributing to the overall performance and durability of electronic products. Additionally, as the demand for miniaturization increases, plastic welding provides a solution for joining small and intricate parts with precision.
Environmental Impact
One of the most compelling aspects of plastic welding is its positive impact on the environment. By facilitating the repair and recycling of plastic components, plastic welding contributes to the reduction of plastic waste. Instead of discarding damaged items, they can be repaired through plastic welding, extending their lifespan and minimizing the need for new production. This aligns with the growing global focus on sustainability and reducing the environmental footprint of various industries.
Conclusion
Plastic welding has emerged as a transformative technology with diverse applications across industries. From enhancing the structural integrity of automotive components to ensuring the cleanliness of medical devices, plastic welding offers efficient and sustainable solutions. As industries continue to prioritize environmentally friendly practices, the role of plastic welding is likely to expand, driving innovation and contributing to a more sustainable future.